German Scientists Have Developed A Helmet With A Shaking Sensor
Researchers from the Fraunhofer Institute for System Strength and Reliability (Germany) have developed an innovative helmet for construction equipment drivers that reduces the risk of serious injuries and occupational diseases.
The helmet is addressed to drivers of machines with difficult operating conditions – excavators and bulldozers. A piezoelectric sensor in the form of a thin film of aluminum-coated polypropylene foam is built into the internal fastening strap of the helmet, which encircles the upper part of the head. The piezoelectric effect means the occurrence of a measurable electrical signal when physical deformation occurs: the greater the deformation, the higher the voltage.
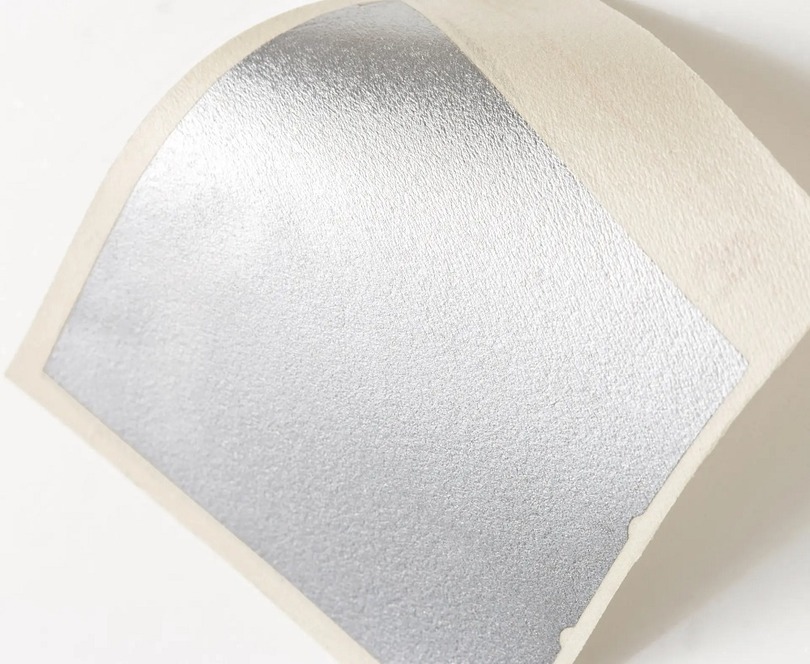
While driving, the driver experiences shaking, the sensor is deformed and generates signals. The voltage and frequency of these signals are transmitted to the body module, which transmits the information to the computer. The data received by the computer is analyzed, and if the vibration reaches a dangerous level, the driver receives a warning. Then he can take a break and, for example, try to correct the situation by attaching damping elements to the seat.
The developers note that the sensor can be used not only to monitor the driver’s condition, but also at the design stage of construction equipment, allowing sources of strong vibration to be identified and eliminated even before the production of the machines begins.